User Case Study:
Using MapleSim for Mechatronics and Control at UCLA
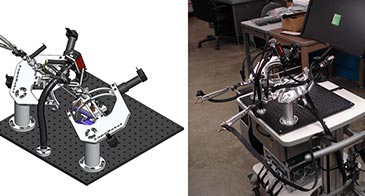
Challenge
At the University of California Los Angeles (UCLA), the Mechatronics and Control Laboratory performs research across a range of control-based applications, including machining, engine control, and nanopositioning. They were looking for software tools that would give them a better dynamic understanding of their systems, in order to develop more precise controllers and iterate on their development faster than before.
Solution
The research lab team chose MapleSim for their dynamic analysis, giving them accurate, system-level models that could serve as test beds for both control development and educational purposes.
Result
By using MapleSim, the team was able to further their development and understanding for a variety of their mechatronics and control projects. In some situations, MapleSim provided the ability to explore their machine dynamics and evaluate control strategies faster, and for other applications, the team used MapleSim to better teach control concepts to their students using interactive models.
In almost every aspect of life today, new and complex technologies exist to improve our quality of life. While these technologies can be very different, they often share a single origin: research labs in academic institutions. These labs, such as the Mechatronics and Control Laboratory at the UCLA, develop and refine new technologies for future applications across industries.
As the head of the Mechatronics and Control Laboratory, Professor Tsu-Chin Tsao helps guide his team’s research, mostly consisting of control-based applications for precision machining, engine control, and nanopositioning. For the design and control of precise machinery, simulation-based tools provide key information about how the machine itself will perform under various operating conditions. Better simulation data has a direct impact on how easily and precisely control strategies can be developed.
As part of their research and education mandate, the team recently adopted MapleSim, the simulation and modeling tool from Maplesoft, in order to create dynamic models of their research projects. With these dynamic models from MapleSim, the team could more easily investigate how their products would perform in different circumstances. The simulation results have helped the team develop better control strategies for various projects, and have served as an effective education tool to demonstrate concepts for their students. Three different projects are highlighted below, outlining their development and testing with MapleSim.
Iterative Learning Control of Robot Manipulators
Trajectory tracking of robot manipulators is a critical technology across several industries, as it has applications in many manufacturing processes, such as laser cutting, welding, polishing, and glue dispensing. The repeated nature of these tasks makes iterative learning control (ILC), a strategy that uses prior trial information to improve subsequent trials, a promising technique for better control strategies. Most industrial robots use geared motors for their low cost, high torque output, and compact sizes. As a consequence of using geared motors, the changing external torque is mitigated by the gear reduction, allowing the team to model the manipulation as a Single Input, Single Output (SISO) system.
Figure 1: The MapleSim model for the RH-12 Robot Manipulator, showing both the multibody model, and the design of a single Feed Drive subsystem.
In this study, the team evaluated whether an ILC strategy could be applied to improve the tracking and control performance [1]. To accelerate the convergence speed and reduce the required iterations, a dynamic model was developed that uses inverse kinematic data to provide the controller with input data. The developed algorithm was tested on a 6 Degree-of-Freedom (DOF) robot manipulator model constructed in MapleSim (Figure 1). Using the dynamic model from MapleSim, the team also investigated the ILC algorithm under common scenarios that impact the robot’s movement, such as joint elasticity, friction, and gear backlash. The team compared the ILC data to a typical, non-ILC design, and found significant improvements using their ILC algorithms (Figure 2).
Figure 2: Results of Baseline PID tracking performance compared to ILC tracking performance, where (A) is the reference path, (B) is the original PID controller path with deviations (red), and (C) is the ILC algorithm path with almost no distinguishable deviation from the reference path.
Robotic System for Tele-Mentoring and Training in Laparoscopic Surgery
The LapaRobot was introduced as a platform to help trainees safely develop the specific skills required for laparoscopic surgery, which uses fiber optic cables inserted into the abdominal wall with great precision [2]. The LapaRobot system is composed of an expert station and a trainee station which are linked via an internet connection. Embedded actuators allow the trainee station to be driven by an expert surgeon so that a trainee learns proper technique through physical feedback. The surgical tool trajectory and video feed can be recorded and later replayed by a trainee to hone their skills through guided repetition without the need for expert supervision. The system is designed to create a high-fidelity approximation of the surgical workspace, incorporate commercially available surgical instruments, and provide a wealth of high-resolution data for quantitative analysis and feedback.
Figure 3: The LapaRobot surgical system (left) and the CAD model describing various aspects of the design (right).
The kinematic model was constructed in MapleSim for evaluating design requirements such as range of motion. Using the MapleSim CAD Toolbox, LapaRobot CAD information was imported into MapleSim, and the components were connected together with revolute and prismatic joints (Figure 4). With this model, range of motion information could be extracted under a variety of operating conditions. Other properties, such as inertia, motor dynamics, and friction can be incorporated to better simulate overall system dynamics, and facilitate the design of better control algorithms.
Figure 4: The component layout is seen in the MapleSim model (left), and the right arm of the model is seen in the 3-D simulation results window of MapleSim (right).
A Novel Twist and Tilt Multi-Rotor Quadcopter
A novel quadrotor system was developed, drawing on dynamic simulation results from MapleSim [3]. Each propeller on this quadrotor consists of two extra rotational joints, providing twisting and tilting capabilities to the propeller blade, and allowing each propeller to generate thrust in multiple directions (Figure 5). The quadrotor has 12 degrees of freedom (DOF), and is over-actuated in three-dimensional space to provide greater control. Compared with traditional under-actuated quadrotors, the twisting-tilting quadrotor is capable of tracking trajectories while maintaining any desired orientation, which provides greater flexibility during movement with better energy efficiency.
Figure 5: The configuration of a single propeller, highlighting the twisting and tilting actuators.
Using MapleSim, the dynamics of each individual component on the quadrotor was evaluated with simulation results. The dynamics of joint servo motors as well as propeller motors are included in the model, and locomotion sensors for the system were added where necessary. The complete MapleSim model was then exported as a Simulink S-Function block using the MapleSim Connector to develop the control algorithms. To test the system, a contact probe was attached underneath the quadrotor to provide contact force feedback. Using this feedback, the quadrotor performance was simulated during simple inspection tasks on varying surfaces (Figure 6).
Figure 6: The 3-D model in MapleSim, used to visualize the quadrotor performance during various simulations.
Going Forward
By using MapleSim, Professor Tsao and his team have developed new methods for developing, testing, and training within the Mechatronics and Control Laboratory at UCLA. These projects have benefited from different features of MapleSim, from visualization capabilities to model export connectivity, and helped both the research and education goals of the lab. Visit Professor Tsao’s website to learn more about the projects underway at the Mechatronics and Control Laboratory.
References
Contact Maplesoft to learn how Maple and MapleSim can help with your projects